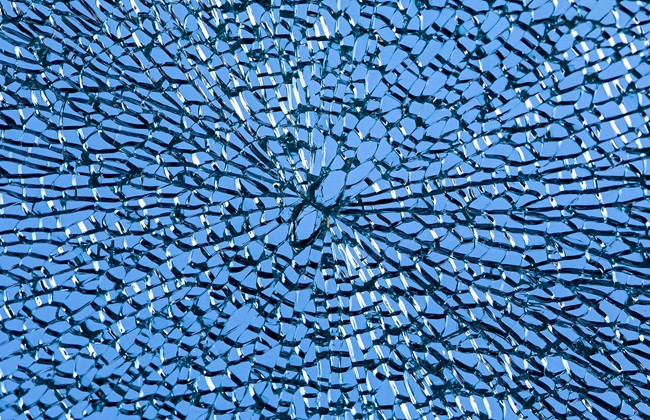
13 Nov Nickel Sulphide Inclusion and Spontaneous Glass Breakage
FAST FACTS
- Nickel Sulphide (NiS) Inclusion, leading to spontaneous glass breakage is a worldwide issue and cannot be blamed on any one country.
- This is not due to cheap imported glass; this is a global issue.
- ALL new buildings that have Low E coatings and or reflective coatings, require the glass to be imported from overseas. Over 90% of new high-rise and low-rise buildings have coatings of some kind. Therefore all of this glass is imported from overseas.
- NO coated glass is made in Australia and production ceased in 2014 due to labour and other factors contributing to no longer being able to be competitive in this market. So ALL coated glass is from overseas – therefore, this has no impact on Australian Jobs.
MORE DETAIL
Nickel Sulphide Inclusion is a phenomenon in the manufacturing of toughened glass, where nickel contaminants in the glass “melt” react with sulphur. This inclusion can lead to a time dependent failure of the glass, where the Nickel Sulphide (NiS) can grow over a period of 1 to 20 years and eventually cause sufficient localised stress to propagate cracks and potentially result in the glass breaking spontaneously without warning. The industry acknowledges this as a type of fatigue or failure that can cause spontaneous fragmentation of toughened and heat-soaked glass, often being unavoidable. When failure occurs due to these inclusions, the glass shatters completely into small pieces as it is designed to do to prevent any large pieces of glass causing harm.
All of the flat glass that you will see in high-rise buildings are produced through a process called “float process”. In this process, molten glass is poured onto a bed of molten tin, forming a continuous ribbon. As the glass cools and solidifies, it is carefully annealed to relieve internal stresses. It is at this early stage of the glass manufacturing process where the Nickel Sulphide inclusion is introduced. Since all of the float glass installed in the buildings are manufactured in the same manner, there is no exception to the possibility of Nickel Sulphide inclusion problem occurring throughout the manufacturing process no matter which country it is produced.
It is important to remember that numerous types of undesirable components known as inclusions are inherent in the manufacturing of flat glass. The Glass Association of North America (GANA) recognizes around 50 different forms of dirt or other inclusions, however nearly all of them are considered safe. The lone exception is Nickel Sulphide, which is a great concern in tempered glass. The building up of Nickel Sulphide Inclusion remains a great concern in the glass industry because there is no current technology that can prevent its formation.
At different temperatures, Nickel Sulphide, like many other compounds, occurs in distinct phases, the alpha-phase and the beta-phase. Nickel Sulphide is stable in the beta-phase at temperatures below 715⁰F (379⁰C) and stable in the alpha-phase above this temperature.
Annealed glass may contain Nickel Sulphide Inclusions that remain stable in their beta-phase. However, it undergoes a transformation into its alpha-phase throughout the tempering process due to its stability at elevated temperatures. However, the rapid cooling during the tempering process does not provide enough time for the Nickel Sulphide to come back to its beta-phase. As a result, the inclusions are “trapped” in the glass during their high-temperature alpha-phase.
Once the glass has cooled below the phase change temperature, the Nickel Sulphide Inclusion attempts to re-enter its lower energy beta-phase. This process can take months or years for “trapped” inclusions. This would have no effect on glass if the Nickel Sulphide did not increase in volume by 2-4% when it transitioned from alpha-phase to beta-phase. This expansion generates localised tensile stresses at the glass Nickel Sulphide Interaction surface that are expected to be as high as 125,000 psi (860 MPa), which is sufficient to generate microcracking. In the glass’s core tension zone, these microcracks are spread by stress concentrations at the tip of the crack until the structure of the glass is entirely undermined and the tempered glass experiences its distinctive shattering, resulting in the seemingly spontaneous breakage.
Written by Eleazar Salut, Head of Engineering BEng (ChemEng)